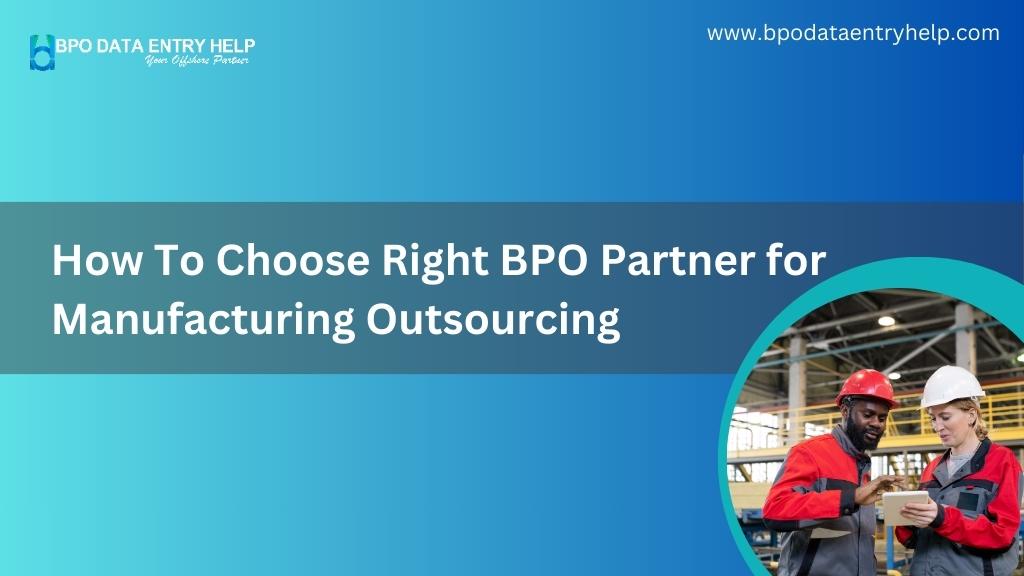
In the constantly evolving era of manufacturing, businesses are continuously looking for methods to enhance their operations and mitigate costs while maintaining high-quality standards. A proven strategy that has attained significant progress over the last few years is business process outsourcing (BPO) in manufacturing. The world of manufacturing is now characterized by agility, efficiency, and relentless pursuit of excellence. To succeed in this dynamic environment, businesses are turning to BPO partners who bring a wealth of experience, expertise, and innovation to the table. Therefore, choosing the right BPO partner for your outsourcing requirements is significant.
Business Process Outsourcing in the manufacturing industry is an effective strategy that involves outsourcing certain business tasks to expert service providers. Usually, these service providers will be from low-cost regions that offer cost-effective solutions without any compromise on quality. As a result, the manufacturing businesses are able to concentrate on their core competencies while having the advantage of improved efficiency and mitigated operational overheads.
BPO in Manufacturing
To make a strategic decision about selecting the appropriate manufacturing BPO provider, it is necessary to learn what Manufacturing BPO entails. Manufacturing BPO comprises an extensive range of processes within the manufacturing industry, including:
Supply Chain Management: Firstly, this entails outsourcing tasks associated with procurement, inventory management, and logistics to enhance the supply chain. Consequently, this results in a simplified and cost-effective supply chain.
Quality Control Assurance: Secondly, BPO partners can deliver extensive quality control services to ensure that the products satisfy the highest standards. Therefore, this confirms the quality and reliability of your manufactured goods.
Production Support: Thirdly, tasks, including assembly, packaging, and labeling, can be outsourced to enhance production efficiency. As a result, this can improve your manufacturing workflow.
Data Management: Additionally, managing and processing bulk volumes of manufacturing data, including product specifications and customer orders, can be a resource-intensive task. Outsourcing this part of your operations can result in enhanced data management and analysis.
Customer Support: Furthermore, outsourcing customer support services guarantees responsive and effective customer interactions. This can improve customer satisfaction and loyalty.
Now that we have learned about BPO in the manufacturing industry, so let’s dive into the critical factors to consider when choosing the right BPO partner for your manufacturing outsourcing requirements.
Key Factors to Consider While Choosing the Right Manufacturing BPO Partner
- Industry Experience and Expertise
While considering potential BPO partners, it is vital to evaluate their industry experience and expertise. Always approach providers who have a proven track record in the manufacturing sector. Especially look for those who possess a thorough understanding of your particular area within the vertical. Experienced service providers are more likely to offer tailored solutions that satisfy your distinct requirements.
- Quality Standards and Certifications
Quality is an important factor to consider in manufacturing, and your BPO partner should uphold the highest standards. Also, know about their quality control processes, certifications, like ISO, and any industry-specific quality benchmarks they stick to. Furthermore, always ensure that the partner has a strong quality assurance framework in position to assure the constant delivery of high-quality products and services.
- Technological Capabilities
In the current era of digitalization, technology has a vital role in manufacturing. Always ensure that your BPO partner has access to cutting-edge technologies and tools significant to your manufacturing processes. Using state-of-the-art technologies like automation, data analytics, and IoT (Internet of Things) can remarkably increase efficiency and productivity.
- Scalability and Flexibility
Manufacturing demands can fluctuate due to market dynamics. Therefore, your selected BPO partner should offer scalability and flexibility to accommodate your varying needs. Whether it’s increasing production volumes or adapting to changes in product specifications, your partner should have the capacity to scale operations accordingly.
- Location and Infrastructure
Always consider the geographical location of your BPO partner carefully. Also, factors such as proximity to your manufacturing facilities, transportation infrastructure, and political stability in the region can affect logistics and supply chain management. Additionally, check whether the partner’s location fits with your strategic goals.
- Data Security and Privacy
Data security is crucial, especially when addressing sensitive manufacturing data. Always ensure that your BPO partner has strong data security measures in place, like encryption protocols, access controls, and compliance with data privacy regulations like GDPR (General Data Protection Regulation).
- Cost-effectiveness
While cost reduction is an important reason for outsourcing, it is mandatory to strike a balance between cost-effectiveness and quality. Therefore, analyze the cost structure provided by potential partners, including all concerned fees and charges. A transparent pricing model will assist you in making an informed decision.
- Communication and Collaboration
Every outsourcing partnership requires effective communication and collaboration to be successful. Therefore, assess the partner’s communication channels, responsiveness, and willingness to collaborate closely with your in-house teams. Because clear and open lines of communication are necessary for resolving issues promptly and aligning with project objectives.
- References and Client Testimonials
Further, request references and client testimonials from the BPO partner. After all, knowing about the experiences of other companies that have worked with the provider can provide valuable insights into their capabilities, reliability, and customer satisfaction levels.
- Compliance with Regulations
The manufacturing industry operates under a range of regulations spanning both national and international levels. It’s essential to confirm that your BPO partner possesses a deep understanding of the compliance demands specific to your sector, encompassing standards related to product quality, safety, and environmental impact.
Now that we’ve outlined the critical considerations for choosing the right BPO partner for your manufacturing outsourcing needs, let’s explore a step-by-step selection process:
The Selection Steps
- Define Your Objectives
The initial step is to clearly define your outsourcing objectives, including the distinct processes or tasks you aim to outsource and the desired outcomes.
- Research Potential BPO Partners
Secondly, always conduct thorough research to identify potential BPO partners. You can utilize industry networks, online directories, and referrals to create a list of candidates.
- Evaluate Experience and Expertise
Evaluate each potential partner’s industry experience and expertise. Also, consider reviewing case studies and client references to gauge their performance.
- Review Technological Capabilities
Evaluate the technological potentials of each partner, ensuring they align with your manufacturing processes and requirements.
- Request Proposals
Request detailed proposals from shortlisted partners, outlining their approach, pricing structure, and service-level agreements (SLAs).
- Conduct Site Visits
If possible, try to arrange site visits to evaluate the partner’s infrastructure, facilities, and quality control processes in person.
- Assess Data Security Measures
Examine the data security measures and protocols implemented by each partner to safeguard sensitive information.
- Negotiate Terms and Contracts
Engage in negotiations with the selected partner to finalize terms, pricing, and contractual agreements. Also, ensure all expectations are documented in the contract.
- Monitor Performance
Establish Key Performance Indicators (KPIs) to monitor the partner’s performance constantly, as well as regularly evaluate their adherence to SLAs and quality standards.
- Foster Collaboration
Maintain open and collaborative communication channels with your BPO partner. Regular meetings and feedback sessions can help enhance the partnership.
How Manufacturing Outsourcing Benefits Businesses
Manufacturing outsourcing provides numerous benefits to businesses seeking to simplify their operations. Major among them are:
Cost Reduction: Firstly, assigning the manufacturing outsourcing processes to a BPO provider located in a lower-cost region can remarkably mitigate production costs. Consequently, this can lead to considerable savings for your manufacturing enterprise.
Access to Specialized Skills: Furthermore, businesses can benefit by learning specialized skills and knowledge as the BPO providers have expertise in manufacturing processes. This expertise will help to streamline operations efficiently.
Focus on Core Competencies: This is the key reason why most businesses choose outsourcing. Outsourcing non-core tasks facilitates businesses to focus on their core competencies, such as product development and innovation. Therefore, this strategic decision has the potential to foster innovation and growth.
Scalability: Manufacturing requirements can vary according to market dynamics. As a result, your selected BPO provider should provide scalability and flexibility to house your changing requirements. Whether it is boosting production volumes or adjusting to changes in product specifications, your partner should have the potential to scale operations accordingly.
Saving Time: Additionally, outsourcing laborious tasks can boost production cycles and time-to-market. Consequently, this can offer you a competitive edge in a fast-evolving market.
Outsourcing manufacturing processes through BPO partnerships provides a pathway to accelerated efficiency, mitigated costs, and improved competitiveness in the worldwide market. By taking into account the key factors outlined in this guide and following a structured selection process, you can confidently select the right BPO partner for your manufacturing outsourcing requirements. In the dynamic landscape of manufacturing, selecting the perfect partner can be the catalyst for transformative growth and success. Embrace the potential of Manufacturing BPO and watch your business thrive as you streamline operations, enhance quality, and attain a competitive advantage in the industry. Your manufacturing outsourcing starts with a well-informed decision. Make it count by selecting a BPO partner that aligns with your vision and goals. Elevate your manufacturing processes and embark on a path to excellence with the right BPO partner by your side.
Are you ready to revolutionize your manufacturing process? Look no further than Allianze Infosoft! With a proven track record of providing high-tech manufacturing services, we are here to accelerate your production to new heights. Our team of experts combines cutting-edge technology with years of industry experience to optimize your operations. Whether it is streamlining supply chains, enhancing quality control, or improving cost efficiency, we have got you covered.
Never miss the opportunity to stay ahead in this competitive manufacturing landscape. Partner with BPO Data Entry Help today and take a strong step together for growth, innovation, and success. Connect with us now at [email protected] to discuss your distinct manufacturing requirements and unlock your complete potential.